Advance Your Career with Lean Six Sigma Green Belt Certification
Unlock your potential with our industry-recognized Lean Six Sigma Green Belt Training. Designed for professionals who aim to lead process improvement initiatives, this course equips you with powerful tools to reduce waste, increase efficiency, and deliver high-quality results across any industry.
A Proven Approach to Process Excellence
Six Sigma is a data-driven methodology focused on reducing variation and eliminating defects in processes. It combines statistical analysis with quality management principles to help businesses optimize performance and drive continuous improvement.
About Our International Accreditation
We are an Internationally Accredited Training Provider by the Council for Six Sigma Certification (CSSC). As an Authorized Training Provider in India, we deliver top-tier Lean Six Sigma Black Belt Training, fully aligned with industry standards and globally recognized certification.
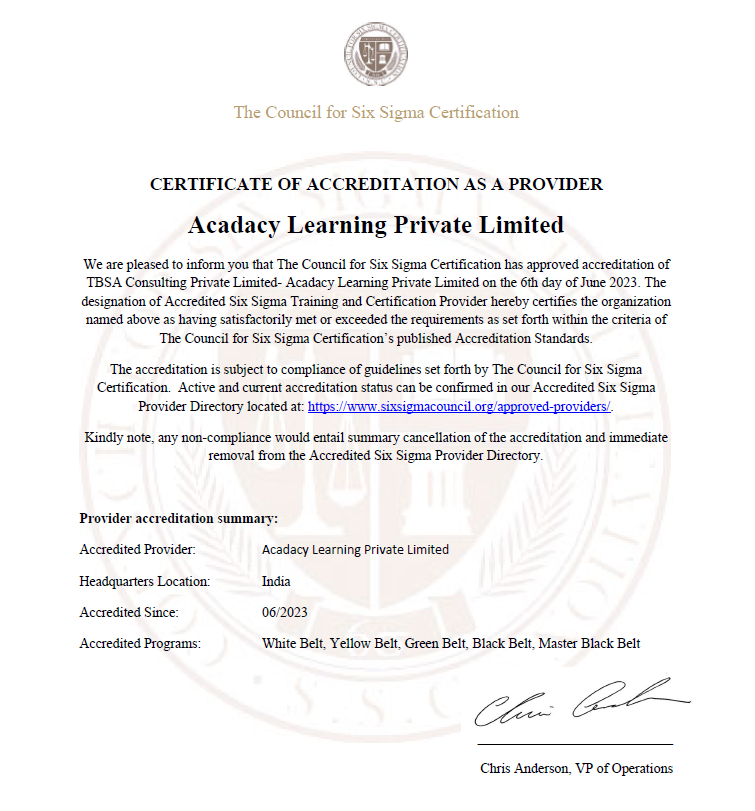
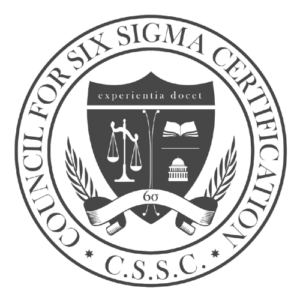
Earn a Lean Six Sigma Green Belt Certificate & Digital Badge
Upon successfully completing of the course you will receive a certificate and digital badge to showcase your skill milestones on Social Media.
A formal recognition of your achievement, perfect for adding to your resume or LinkedIn profile.
A shareable, verified badge that you can proudly display on your social media profiles and professional networks.
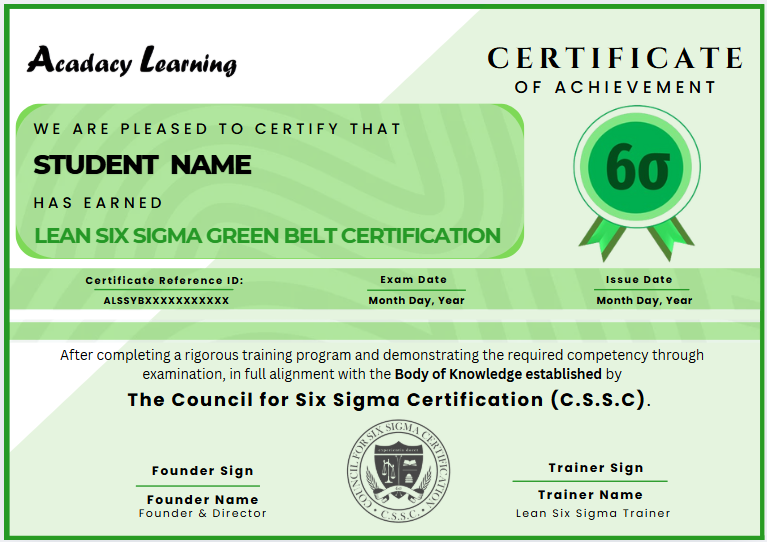
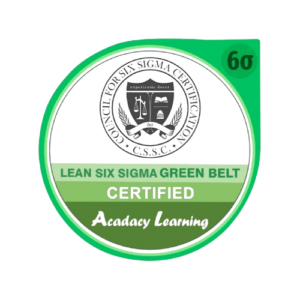
Why Choose Our Lean Six Sigma Green Belt Training & Certification?
Our Lean Six Sigma Black Belt Training is Globally Accredited and Aligned with the Council's Body of Knowledge
- Accreditation: Our training program is internationally recognized and accredited by the Council for Six Sigma Certification (CSSC), ensuring you receive high-quality education that meets global industry standards.
- Comprehensive Curriculum: Our course curriculum is carefully crafted to match the Body of Knowledge (BOK) defined by the CSSC, ensuring that you are equipped with all the tools and techniques needed to excel as a Black Belt.
- Global Standard: This program provides you with the knowledge and skills that are relevant and respected in organizations worldwide, from manufacturing to healthcare.
- Expert Trainers with Real-World Experience: Learn from industry experts with years of practical experience, who guide you through every step of the process and ensure that you are job-ready upon certification.
- Hands-On Learning & Projects: Apply your knowledge through real-world case studies and projects, gaining practical experience that you can immediately implement in your career.
- Flexible Learning Options: With online and offline training programs, you can learn at your own pace, making it convenient to fit into your busy schedule.
- Lifetime Access to Course Materials: Once enrolled, you’ll have lifetime access to all course materials, updates, and additional resources, ensuring you remain ahead in your career.
- Ongoing Support and Networking: As an Acadacy Learning graduate, you gain access to a supportive network of Lean Six Sigma professionals, ensuring continuous learning and career growth.
Learn DMAIC Problem-Solving Methodology
DMAIC - A Step-by-Step Framework for Process Improvement
DMAIC (Define, Measure, Analyze, Improve, Control) is the core of Six Sigma. You will master each phase through practical exercises and real-life examples, learning how to:
Define problems clearly
Measure process performance
Analyze root causes
Improve processes with data-backed solutions
Control and sustain improvements over time
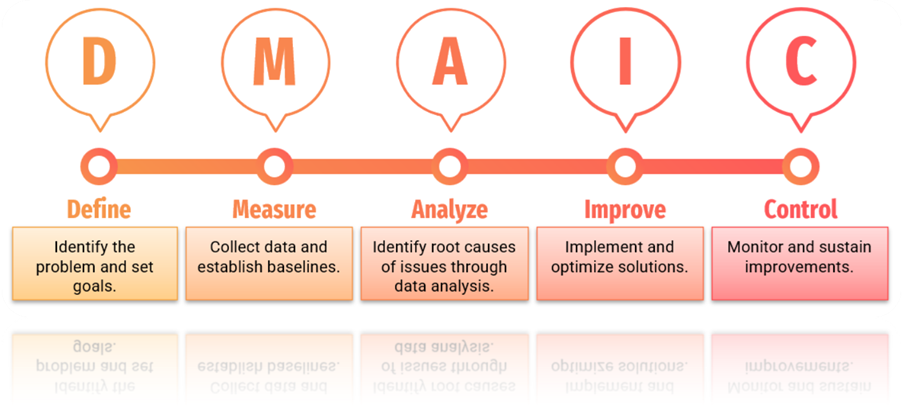
The DMAIC Process: Your Roadmap to Success
- Define – Identify the problem, set clear objectives, and understand customer requirements.
- Measure – Collect and analyze data to assess the current process performance.
- Analyze – Pinpoint root causes of problems using powerful analytical techniques.
- Improve – Develop and implement effective solutions to enhance process performance.
- Control – Establish systems to monitor and sustain improvements over time.
What Our Students Have to Say
See how our training program has transformed careers. Our students’ success is a true reflection of the skills, confidence, and expertise they gained. Hear directly from them!
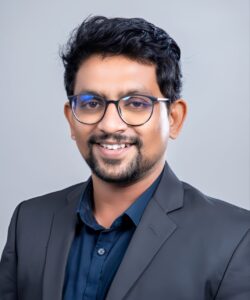
Krishna Chaitanya G
I have completed Lean Six Sigma Black Belt training. So far, the training has been very lively and practical.
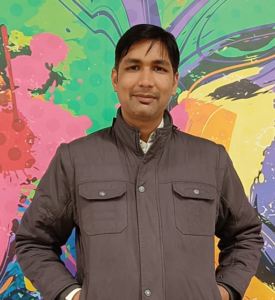
Vivekanand Singh
Lean Six Sigma Green Belt
It is an amazing learning experience with great content. The trainer has a fantastic skill to elaborate on every topic very deeply and effectively.
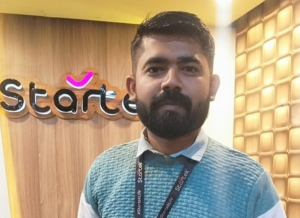
Chetan Parihar
Lean Six Sigma Green Belt
The practical approach, including hands-on projects and case studies, enhanced my ability to apply Six Sigma principles effectively. This certification has significantly improved my skills in driving process excellence and delivering measurable results, making a positive impact on my professional growth and organizational success.
I highly recommend this certification to anyone aiming to enhance their expertise in quality management and operational excellence.
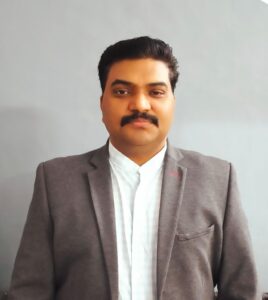
Bhushan Jarodia
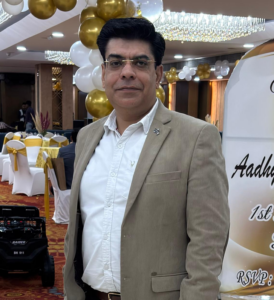
Parveen Kumar
Manager
The Lean Six Sigma Green Belt Training was fantastic! The course was easy to follow, and I could immediately apply what I learned at work. The instructor was really knowledgeable and supportive, making everything clear. Since completing the certification, I’ve felt more confident leading projects. Highly recommend it to anyone wanting to improve their skills and career
Lean Six Sigma Green Belt Course Curriculum
Define Phase
- Project Selection and Chartering: How to choose the right project and develop a project charter.
- Voice of the Customer (VOC): Understanding customer needs and translating them into specific project requirements.
- Problem Definition: Identifying the problem statement, goals, and objectives.
- Stakeholder Analysis: Identifying stakeholders and understanding their needs and expectations
- Project Charter Creation: Establish your project charter team.
Measure Phase
- Data Collection Plan: Designing a plan to collect relevant data that aligns with the project objectives.
- Data Types and Sampling Techniques: Understanding different data types (continuous vs. discrete) and sampling methods.
- Process Performance Metrics: Identifying and defining key performance indicators (KPIs).
- Measurement System Analysis (MSA): Evaluating the reliability and accuracy of measurement systems.
- Baseline Performance: Establishing current performance metrics to compare against after improvements.
- Process Capability Analysis: Analyzing how well the current process meets desired outcomes.
Analyze Phase
- Root Cause Analysis: Identifying the root causes of the problem using tools like Fishbone Diagrams, 5 Whys, and Pareto Analysis.
- Statistical Analysis: Using tools like hypothesis testing, regression analysis, and correlation analysis to identify patterns and relationships in data.
- Failure Modes and Effects Analysis (FMEA): Identifying potential failure points and assessing their risks.
- Hypothesis Testing: Forming hypotheses about the relationships between variables and testing them using statistical methods such as t-tests, chi-square tests, ANOVA, etc.
Improve Phase
- Brainstorming and Solution Generation: Generating and evaluating potential solutions to address the root causes.
- Solution Implementation: Developing action plans and implementing the selected solutions.
- Pilot Testing: Testing solutions on a small scale before full implementation to ensure effectiveness.
- Cost-Benefit Analysis: Assessing the potential savings, ROI, and costs associated with the proposed improvements.
Control Phase
- Control Plans: Creating a detailed plan to monitor and control the improved process.
- Sustaining Improvements: Implementing strategies to ensure continuous monitoring and sustaining improvements over time.
- Control Charts: Using charts like X-bar, R-charts, and p-charts to monitor process stability.
- Standard Operating Procedures (SOPs): Developing SOPs to standardize new processes and maintain improvements.
- Training and Knowledge Transfer: Ensuring that the team is trained and equipped to maintain the new processes.
Frequently Asked Questions (FAQ) - Lean Six Sigma Green Belt
Q1: Is this certification recognized internationally?
Yes. Our certification aligns with international standards and is respected across industries worldwide.
Q2. Do I need prior Six Sigma experience?
This course is designed for beginners and professionals alike.
Q3. Will I get support during the course?
Absolutely. Our trainers and support team are available throughout your learning journey.
Q4. What are the benefits of becoming a Lean Six Sigma Green Belt?
Becoming a Lean Six Sigma Green Belt offers numerous benefits:
Career Advancement: Stand out with a globally recognized credential valued across industries.
Higher Earning Potential: Certified professionals often command higher salaries and more leadership roles.
Problem-Solving Expertise: Gain practical skills to identify inefficiencies and implement sustainable solutions.
Organizational Impact: Lead projects that reduce costs, improve quality, and enhance customer satisfaction.
Foundation for Further Growth: It’s a stepping stone to advanced certifications like Black Belt and Master Black Belt.
Q5. How long does it take to earn the Lean Six Sigma Green Belt?
We do cover all tools and techniques in Lean Six Sigma Green Belt Training & Certification
- We cover the entire syllabus in 28 to 32 hours
- We also cover a consecutive 4-day training, 8 hours each day, to cover the entire curriculum
- We can also schedule training as per your flexible timing on weekdays
- Full-time programs may take less time but require more intense focus.
Q6. What prerequisites are required for the Green Belt certification?
There are no strict prerequisites for Lean Six Sigma Green Belt training. However, the following are recommended to help you get the most out of the course:
Basic understanding of business processes or operations
Familiarity with Excel or basic data analysis tools (not mandatory but helpful)
Interest in problem-solving and continuous improvement
For professionals: Ideal if you’re in roles such as quality assurance, operations, project management, or engineering
Q7. What skills will I gain during the Lean Six Sigma Black Belt training?
Skills You Will Gain
Process improvement & waste reduction
Data analysis & problem-solving
DMAIC project management
Root cause analysis tools (5 Whys, Fishbone)
Quality control & process control tools
Team collaboration & leadership
Effective communication of data insights
Q8. Can Lean Six Sigma Green Belts work in any industry?
Yes! Lean Six Sigma principles can be applied to virtually any industry, including:
- Manufacturing
- Healthcare
- Information Technology (IT)
- Financial Services
- Education
- Government
- Retail and Service sectors
Let’s Talk Learning
Ready to take the next step in your learning journey?
We’re here to help!
Call Us
If you prefer to speak with us directly, give us a call:
M: +91 73037 34433
Email Us
For general inquiries, feedback, or support, you can email us at:
info@acadacy.com
We value your thoughts and aim to respond to all inquiries promptly.
Thank you for reaching out to us!