Total Quality Management (TQM)
Total Quality Management (TQM) is a comprehensive management approach focused on improving quality across all organizational processes. It integrates all quality-related functions and processes throughout the company to deliver superior customer satisfaction.
Total Quality Management is a company-wide approach to continuous improvement, focused on meeting customer needs, enhancing performance, and reducing errors across all departments.
What is Total Quality Management?
TQM is a structured system for managing quality based on the participation of all organization members. It emphasizes continuous improvement, data-driven decision-making, and customer focus to achieve long-term success.
TQM Principles
TQM is based on eight core principles:
Customer Focus
Total Employee Involvement
Process-Centered Approach
Integrated System
Strategic & Systematic Approach
Continual Improvement
Fact-Based Decision Making
Communication
Earn Certification & Digital Badge
Upon successfully completing of the course you will receive a certificate and digital badge to showcase your skill milestones on Social Media.
A formal recognition of your achievement, perfect for adding to your resume or LinkedIn profile.
A shareable, verified badge that you can proudly display on your social media profiles and professional networks.
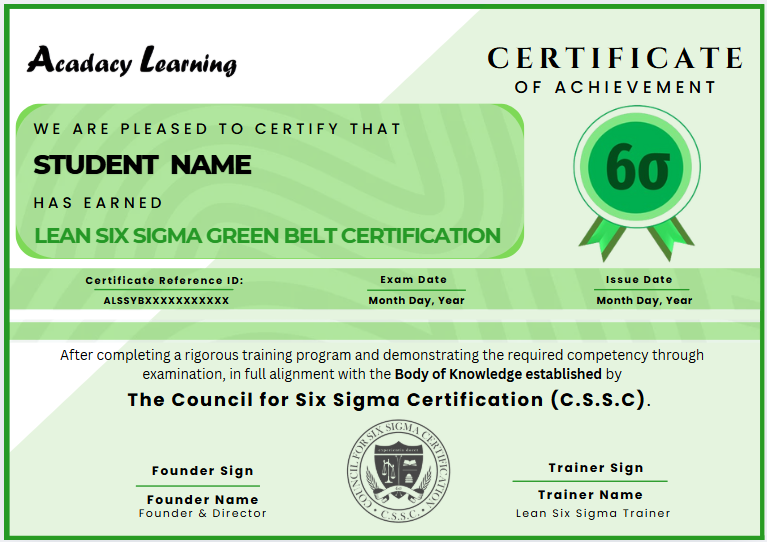
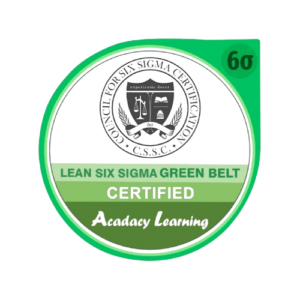
Earn Certification & Digital Badge
Our course combines expert instruction, real-world tools, flexible learning, and a globally recognized certificate to help you lead quality improvements with confidence.
What You Will Learn
You’ll learn the foundations of TQM, key tools for process improvement, leadership in quality management, and how to align quality efforts with business goals.
What You Will Learn
- PDCA Cycle (Plan-Do-Check-Act): A continuous improvement loop used to test and implement changes in processes.
- Pareto Chart: A bar graph that identifies the most significant factors contributing to a problem (based on the 80/20 rule).
- Cause-and-Effect Diagram (Ishikawa/Fishbone): Used to identify root causes of problems by categorizing potential sources (e.g., people, process, materials).
- Check Sheet: A structured, simple form used to collect data in real time and identify patterns.
- Histogram: A graphical representation showing the frequency distribution of data for variation analysis.
- Control Chart: Monitors process behavior over time and helps detect trends or out-of-control conditions.
- Scatter Diagram: Plots two variables to identify potential relationships or correlations.
- Flowchart (Process Mapping): Visual representation of a process, helping identify steps, bottlenecks, and improvement areas.
- 5 Whys: A root cause analysis method that involves asking “Why?” multiple times until the underlying issue is identified.
- 5S Methodology: Organizes workspaces for efficiency: Sort, Set in order, Shine, Standardize, Sustain.
- Benchmarking: Comparing processes and performance metrics with industry bests or competitors.
- Kaizen (Continuous Improvement): A philosophy encouraging regular, incremental improvements involving all employees.
- Value Stream Mapping: A lean-management method for analyzing the current state and designing a future state for the series of events that take a product from start to finish.
- Root Cause Analysis (RCA): A structured approach to identify the underlying causes of issues, not just the symptoms.
Pre-requisite
No specific background required. Open to professionals, students, and business owners with interest in quality and process improvement.
Frequently Asked Questions (FAQ) - Lean Six Sigma Green Belt
Q1: What is Total Quality Management (TQM)?
TQM is a company-wide approach that focuses on continuous improvement, customer satisfaction, and involving all employees in quality initiatives.
Q2. Who is this training suitable for?
This course is ideal for professionals, managers, students, and business owners seeking to improve quality and efficiency in their organizations.
Q3. Do I need prior experience to take this course?
No prior experience is required. The training starts with the basics and gradually builds up to more advanced concepts.
Q4. Is this certification recognized globally?
Yes, the certification is widely accepted and demonstrates your commitment to quality and continuous improvement.
Q5. What is the duration of the course?
The course is typically self-paced and online, can be completed in 6 to 8 hours, depending on your learning speed.
Q6. Will I receive a certificate after completion?
- Yes, you’ll receive a verifiable certificate and a digital badge that you can add to LinkedIn or your resume.
Q7. Can I access the course materials after finishing the training?
- Yes, you’ll have lifetime access to all training resources, including updates and additional learning materials.
- We will also provide PDUs for entire course curriculum
Q8. What kind of support is available during the course?
You’ll have access to trainer support, discussion forums, and optional live Q&A sessions to help with any questions.
Let’s Talk Learning
Ready to take the next step in your learning journey?
We’re here to help!
Call Us
If you prefer to speak with us directly, give us a call:
M: +91 73037 34433
Email Us
For general inquiries, feedback, or support, you can email us at:
info@acadacy.com
We value your thoughts and aim to respond to all inquiries promptly.
Thank you for reaching out to us!